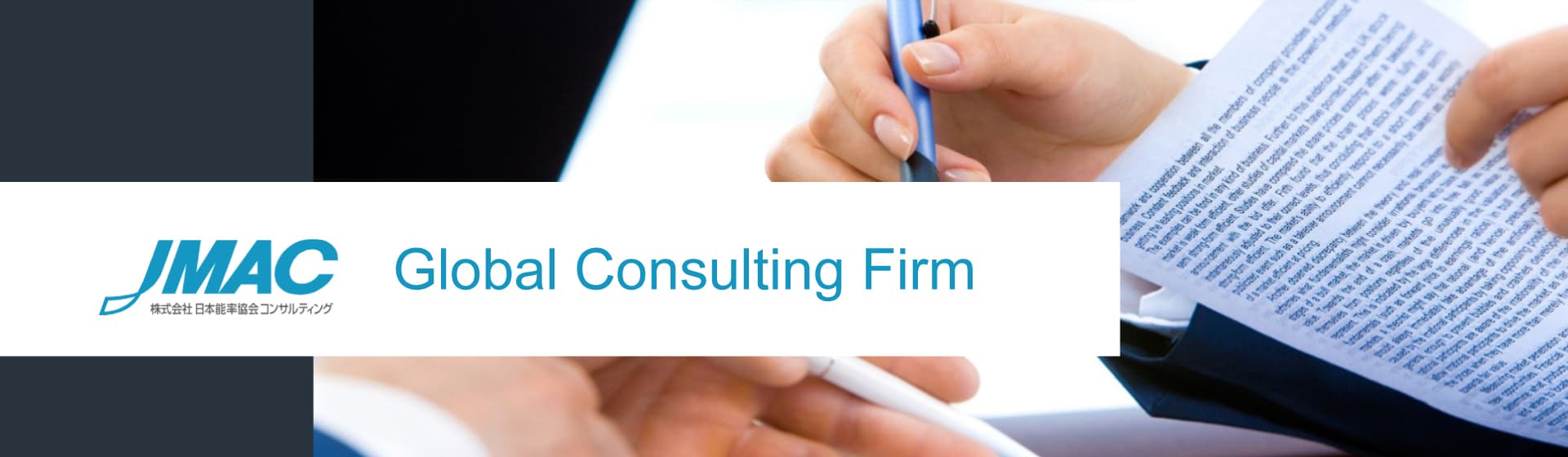
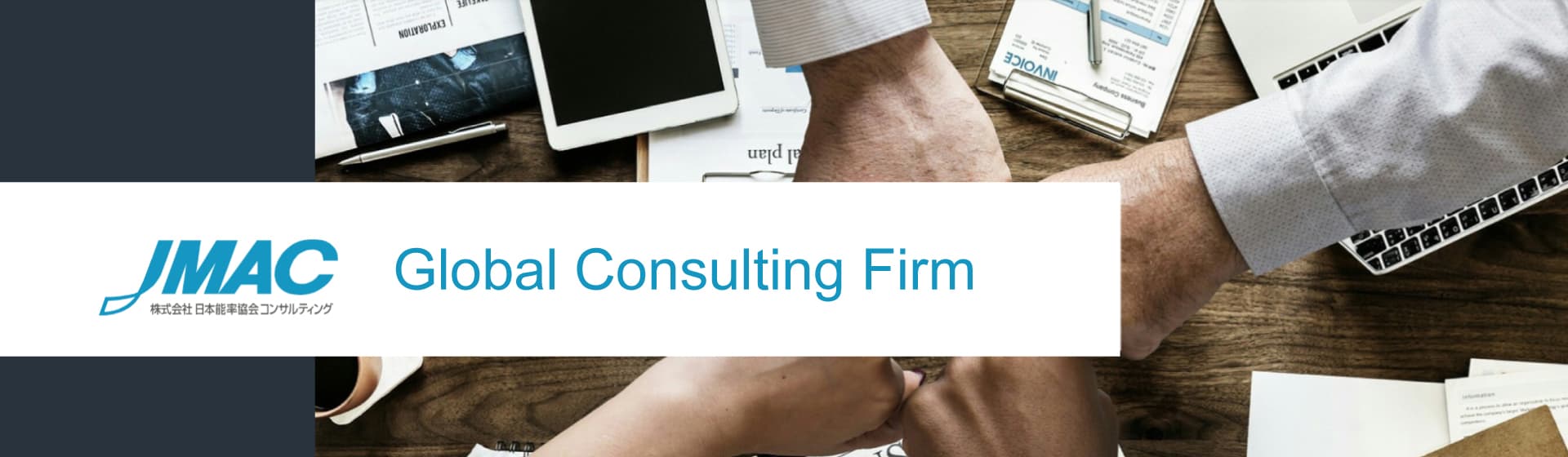
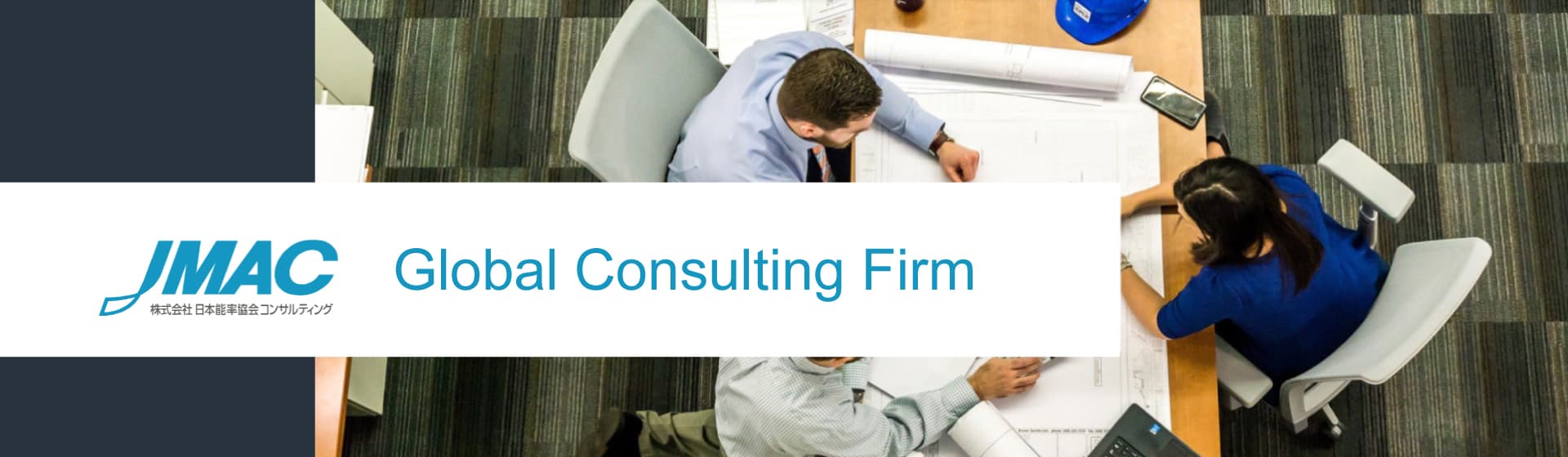
自動車産業から生まれた、効率的な生産の仕組み
皆さんは「Lean Manufacturing(リーン生産方式)」や「トヨタ生産方式(TPS)」という言葉を聞いたことがあるでしょうか?これらは、効率的な生産を指向する仕組みのことです。この二つはどのように違うのでしょうか?
TPSとは、トヨタが長年実践してきた様々な取り組みを1970年代にトヨタ生産方式としてまとめ、外部に発表したものです。
一方、リーン生産方式は、1980年代にMIT(マサチューセッツ工科大学)が日本の自動車会社を研究した結果、TPS をベースに色々なコンセプトや手法を取り入れることで誕生しました。
これらの仕組みのゴールは、無駄がなく、仕掛や在庫の少ない工場を達成することにあります。しかし、それに到達するアプローチはTPSとリーン生産方式で少し異なっています。 TPSでは、トヨタが長年にわたって作業の無駄を削り、工程間の仕掛を減らし続けた結果、高い生産性の工場が実現できました。社内で継続的に改善をしていくことが当たり前になっています。
次回以降は、ここで用いられているコンセプトやツールについて、説明をしていきます。
※JMACでは、様々なモデルやフレームワークを使い、異文化ギャップの問題を解決します。
JMACタイランドは、同地で10年以上のコンサルティング実績を有します。
Office
Tel: +66(0)2-168-3037
小田 Oda
Email: Nobuya_Oda@jmac.co.jp